We were one of the first Astréa 42 Smart Electric catamarans delivered by the Fountaine Pajot ship yard. In this post I describe the Smart Electric system as it’s installed on our Astréa 42; the rating and configuration of the Smart Electric components may be different on the other yacht models.
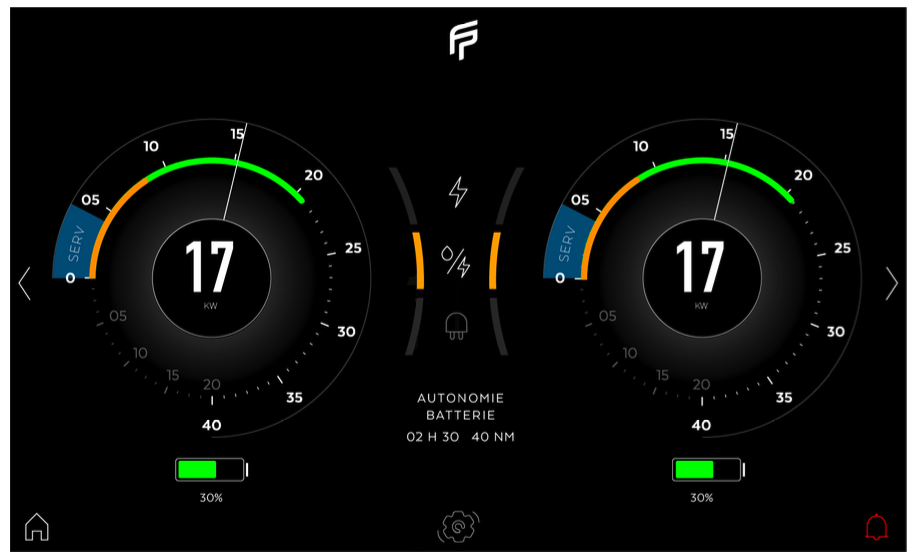
Overview
The following discussion is based on my understanding of the system as an end-user, I apologise if I’ve got something wrong.
The Smart Electric is a hybrid electric catamaran, comprising two pure electric propulsion systems coupled with a single diesel generator. The two propulsion systems, one per side, are fully redundant with each side containing:
- a high voltage lithium iron phosphate (LiFePo4) battery;
- a Smart Electric One Box;
- an Energy Propulsion Management System computer (EPMS);
- an electric motor pod;
- and an optional shore power charger.
Shared across the two sides are:
- a diesel generator;
- a control panel at the nav desk and another at the helm;
- power switches, emergency stop switches and battery bypass switches at the nav desk;
- control levers at the helm;
- solar panels;
- and the 12 volt service battery bank.
The following diagram comes from the user guide and shows the system components.
Equipment Description
The following diagram shows my conceptual understanding of the current flows between the various electrical components. This is a diagram I drew.
- The motor pod is a 25 kW electric motor that is mounted under the hull. It drives a 3 blade, fixed 580×381 propellor manufactured by Maucour. The motor pod provides for both propulsion and hydrogeneration and is manufactured by Alternative Energies (AE).
- The propulsion battery is a 205 volt Lithium Iron Phosphate rated at 21 kWh, manufactured by AE. It weighs 200 kg and is mounted directly above the motor pod, in place of the diesel engine.
- The generator is 16 kW 3 phase, manufactured by Kohler.
- The service battery is a 12 V 450 Ah battery bank consisting of 3 x 150 Ah AGM batteries.
- There are two DC-DC chargers rated at 50 A and manufactured by AE. They connect between the service battery and each propulsion battery.
- A Victron DC-DC charger connects from the service battery to the generator start battery to keep the start battery charged.
- The solar panels are 3 x 400 W manufactured by Sunpower, giving a total of 1.2 kW.
- The MPPTs are Victron, 1 per panel.
- There is an (optional) inverter, manufactured by AE and rated at 6 kW. It is connected to the port propulsion battery and runs the heavier AC loads: on our boat this is the air conditioning, clothes washer and water heater.
- There is a second inverter: a Victron Phoenix 3 kW. This is connected to the service battery and powers the AC outlets and microwave.
- One shore power inlet connects to a Victron charger to primarily charge the service battery.
- Another shore power inlet connects to two (optional) chargers to primarily charge the propulsion batteries. These chargers are rated at 3 kW each and are manufactured by AE.
How the System Works
Batteries & Charging
All electrical consumption comes from the batteries. The service battery provides 12 volt power to the boat, the same as on a diesel boat, as well as AC power via a 3 kW inverter to the outlets and for the microwave. The starboard propulsion battery only powers the starboard motor. The port propulsion battery powers the port motor and provides AC power via a 6 kW inverter to the equipment that on a diesel boat would be run from the generator or shore power; such as: air conditioners, water heater and clothes washer.
The service battery and propulsion batteries connect through 2-way 50 amp DC/DC chargers; one charger per propulsion battery. These allow the propulsion battery to maintain the service battery, in one direction, and in the other direction for any excess charge to flow from the service battery to the propulsion batteries.
The solar panels connect to the service battery, as would any wind generators if installed. These charge sources will service the 12 volt system first with excess charge flowing to the propulsion batteries. The other charging source for the service battery is an AC charger connected to a dedicated shore power inlet. This charger is rated lower than the DC/DC chargers from the propulsion batteries, and is only meant for charging if the Smart Electric system is powered down during winterisation or long absences.
The generator has two functions: charging the propulsion batteries and powering the motors. The generator doesn’t connect to any appliances. For charging, it is normally controlled automatically and will be started when the propulsion batteries fall to a 20% charge level and then shutdown when the batteries are charged. It can be started manually, if required. It will also start when the propulsion system is placed into hybrid mode (more about this later) and will then power the motors with any excess power being used to charge the batteries. It is also possible to have the generator directly power the motors, bypassing the batteries: in this situation the batteries will not be charged. This allows use of the motors when there has been a failure of the propulsion batteries.
The propulsion batteries can also be charged by the electric motors in regeneration mode. In this mode the motor functions as a hydrogenerator, using the water flowing over the propellor to spin the motor to generate a charge. Each motor can generate up to 2 kW for a system total of 4 kW. It’s possible to have 0, 1 or 2 motors enabled for regeneration. It’s also possible to have one motor driving and the other one generating.
The final charge source are the optional AC chargers for the propulsion batteries which are connected to a second dedicated shore power inlet. These chargers are 3 kW each and are adjustable to cater for the rating of the available shore power. Typically, this is how the batteries would normally be charged: charging the propulsion batteries, and charging the service battery via the DC/DC chargers.
The propulsion batteries are not directly connected – they will charge and discharge at their own rate. In operation it is normal to see the two propulsion batteries at different levels of charge.
There are two inverters in the system: the first is a 3 kW inverter that is installed as part of the shore power factory option; and the second is a 6 kW inverter that is available as a Smart Electric option. The 3 kW inverter is powered from the 12 V service battery and supplies power to the lower rated AC appliances such as outlets and microwave. The 6 kW inverter is powered from the port propulsion battery and supplies power to the AC appliance that would normally be connected to the generator and shore power. It is important to realise that no AC appliance is connected to the generator or shore power; all AC power comes from an inverter.
How Other Factory Options were Affected
As much as possible, Fountaine Pajot have made Smart Electric an option that is picked from the list of factory options, the same as picking any other option. Instead of dropping in the diesel engines, the factory drops in an electric motor. For us, there were some side-effects on our other options because of the space required for the Smart Electric components. Over time these issues may be resolved and may not impact future Astréa 42s fitted with Smart Electric.
The generator option is mandatory. The standard generator is 9 kW, but for Smart Electric this is upgraded to 16 kW.
We had requested central diesel heating, but it couldn’t be installed because the install location is taken by a Smart Electric component. We were advised to just use the air conditioners for heating or to arrange an ex-factory installation of a diesel heater.
We had requested our dealer to install 2 kW of solar panels. With the Smart Electric option we had to take either the factory option of 400 W or a Fountaine Pajot Services (FPS) option of 1.2 kW. There is no option to have solar panels fitted by anyone else, and to have more than 1.2 kW. We were also advised that if we went ahead and installed additional solar panels after delivery we would face issues with support and warranty for the Smart Electric. With this being a new technology for FP, I understand and accept that the engineers want to control as many parameters as they can; it makes support and remote fault diagnosis in the field easier. We plan to revisit this in two years time when the warranty finishes and by this time the Smart Electric engineers will be better acquainted with how the technology is performing.
Another side-effect was the location of the water maker. It’s normally fitted in the locker with the generator, but with the much larger generator the water maker needs to be relocated. At the time of writing this still hadn’t been resolved.
Operation Overview
Each motor is operated independently, and the system is split into two sides, starboard and port.
At the nav desk there is the control panel, which is a touch screen. There are also six switches, three for each side: a main power switch; a switch to enable battery-off mode which connects the generator directly to the motor if the battery fails; and, and an emergency stop switch. Turning on the power switch enables the Smart Electric system for that side. Normally when the boat is in use, both sides would be turned on.
The control panel is used to monitor and control the system. It provides information about where power is flowing, the overall state of charge (SOC), and current warning/error notifications. It allows you to manually switch between two of the system’s modes: zero emission (ZE), and hybrid (HY). Shore mode is automatically shown whenever shore power is plugged in and turned on.
ZE mode is when the generator is not being used; HY mode is when the generator is running. The generator automatically starts when either propulsion battery falls below 20% SOC, and the system will automatically switch to HY mode. If the propulsion systems (ie. the motors) are turned off, the generator will charge the batteries until they reach 97% SOC and then be automatically turned off. If either propulsion system is on, the generator first supplies power to the motor and then charges the battery. When the battery reaches 97% SOC the generator will continue running, supplying power to the motor and maintaining the battery at 97%. The generator can be started manually by switching the console to HY mode or by starting the generator from its own console (mounted on the generator). When the generator stops (automatically, manually, or unexpectedly) the system will automatically switch back to ZE mode.
For normal operation, the generator start battery must be turned on and the generator (using its own console) must be switched to Auto mode. If either of these is not on then the Smart Electric system will not switch into HY mode, and the batteries will be damaged if they are allowed to discharge. The system will issue fault notifications if it cannot start the generator.
When being charged from shore power, the system cannot be turned off.
At the helm there is a control panel and the motor control levers. The control panel functions exactly the same as the one at the nav desk. The control levers comprise: a power button to turn the propulsion system (the motors) on and off; two buttons (one for each side) to switch the motor between propulsion and regeneration; and levers to control the amount of power to/from each motor. As with the main system, the motors are controlled independently. The current state of each motor is displayed on the control panel.
When driving the motor, the levers work exactly the same as for a diesel engine. When in neutral an audible ping is emitted to remind you that the propulsion system is on. The levers move easily and may be knocked by someone walking along the side deck or working the winches.
Placing the motors in regeneration mode will create a charge back into the batteries. The amount of charge coming from the motor is increased by pushing the lever forward, up to a maximum of 2 kW, and is dependant on the boat’s speed.
Emergencies
In an emergency, the system can be rapidly shut down using the big red emergency stop buttons at the nav desk. There is one per side. When pressed: propulsion is turned off; the battery is turned off; the inverter is turned off (port side); the DC-DC charger is turned off; and, a fault notification is displayed on the console. If hybrid mode is active and both emergency stop buttons are hit, the generator will be shut down.
If there is a failure of a propulsion battery, it can be bypassed using the battery-off switch at the nav desk (located directly below the power switches) this bypasses the battery and connects the generator directly to the motor.
Noise
Before finishing this post, a word on noise of the motors. They are more noisy than I expected. When engaging and disengaging the motor there is a very obvious shudder that can be both felt and heard. And then as power is applied the noise and vibration will change accordingly. I suspect the reason for most of this is that the motors are directly attached to the hull without any sort of vibration dampening. I think that introducing any sort of vibration dampening would directly affect the drive efficiency of the motor. The noise and vibration is not intrusive and you do quickly stop noticing it.
Maintenance
The generator requires the usual servicing and maintenance that any generator requires.
The motors have anodes attached to the pods, close to the underside of the hull. These are good sized anodes that are readily available (they’re not specific to the motor pod).
No other servicing is required. The maintenance is then the same as any boat electrical system. Keep an eye on connections to ensure they are tight and there is no corrosion; keep an eye out for any deformed insulation on cables, or for signs of sparking on terminals; occasionally check cables and equipment for excessive heat; keep the batteries within their defined limits and monitor them for excessive heat. The biggest cause of fires on boats is the electrical system and the appliances connected to it.
Conclusion
So far we are extremely happy with the Smart Electric system. I think it has been really well thought through and well engineered. I’m keen to see how it goes once we start cruising. It’s also very easy to understand and use. While I may be more technically inclined, I don’t think that a technical understanding of the system is required to operate it and ensure that it’s all working correctly.
I hope this explanation helps anyone interested in the Fountaine Pajot Smart Electric option, and I’m happy to answer any questions you may have, to the best of my ability within the boundaries of what’s installed on Songa and our use of it.
If you are interested in getting a Smart Electric catamaran, then the best place to get the latest information should be your closest FP dealership. If you are in Australia, New Zealand, SE Asia or the South Pacific then get in touch with The Yacht Sales Co or Multihull Solutions as they have a high level of technical expertise in Smart Electric.